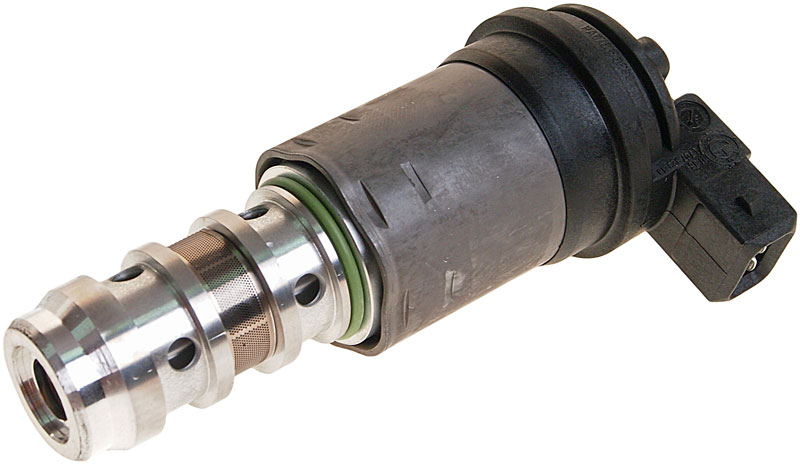
On all types of cars, buses, tractors and special equipment, solenoid valves are widely used to control the flow of liquids and gases. Read about what solenoid valves are, how they are arranged and work, and what place they occupy in automotive equipment in this article.
What is a solenoid valve and where is it used?
A solenoid valve is an electromechanical device for remote control of the flow of gases and liquids.
In automotive technology, solenoid valves are used in various systems:
- In the pneumatic system;
- In the hydraulic system;
- In the fuel system;
- In auxiliary systems - for remote control of transmission units, dump platform, attachments and other devices.
At the same time, solenoid valves solve two main tasks:
- Control of the flow of the working medium - the supply of compressed air or oil to various units, depending on the operating mode of the system;
- Disabling the supply of the working medium in emergency situations.
These tasks are solved by solenoid valves of various types and designs, which needs to be described in more detail.
Types of solenoid valves
First of all, solenoid valves are divided into two groups according to the type of working medium:
- Air – pneumatic valves;
- Fluids – valves for the fuel system and hydraulic systems for various purposes.
According to the number of flows of the working medium and the features of the operation, the valves are divided into two types:
- Two-way - have only two pipes.
- Three-way - have three pipes.
Two-way valves have two pipes - inlet and outlet, between them the working medium flows in only one direction. Between the pipes there is a valve that can open or shut off the flow of the working medium, ensuring its supply to the units.
Three-way valves have three nozzles that can be connected to each other in various combinations. For example, pneumatic systems often use valves with one inlet and two outlet pipes, and at different positions of the control element, compressed air from the inlet pipe can be supplied to one of the outlet pipes. On the other hand, in the EPHX valves (forced idle economizer) there is one exhaust and two intake pipes, which provide normal atmospheric and reduced pressure to the carburetor idling system.
Two-way valves are divided into two types according to the position of the control element when the electromagnet is de-energized:
- Normally open (NO) - the valve is open;
- Normally closed (NC) - the valve is closed.
According to the type of actuator and control, valves are divided into two types:
- Valves of direct action - the flow of the working medium is controlled only by the force developed by the electromagnet;
- Pilot solenoid valves – the flow of the working medium is controlled in part by using the pressure of the medium itself.
In cars and tractors, simpler direct-acting valves are most often used.
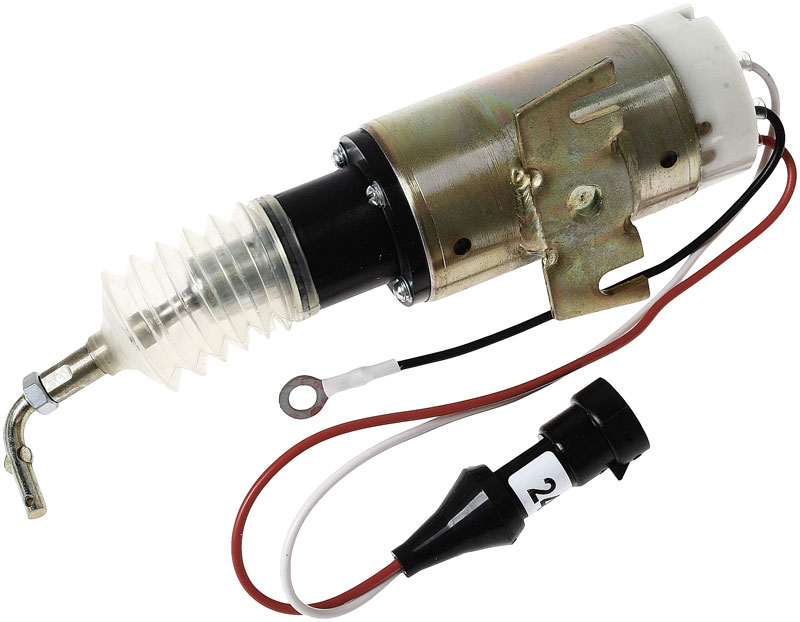
Also, the valves differ in performance characteristics (supply voltage of 12 or 24 V, nominal bore and others) and design features. Separately, it is worth mentioning the valves, which can be assembled into blocks of 2-4 pieces - due to a certain position of the pipes and fasteners (eyelets), they can be combined into a single structure with a large number of inlet and outlet pipes.
The general structure and principle of operation of solenoid valves
All solenoid valves, regardless of type and purpose, have essentially the same design, and they have several main components:
- Electromagnet (solenoid) with an armature of one design or another;
- Control/locking element (or elements) connected to the armature of the electromagnet;
- Cavities and channels for the flow of the working medium, connected to fittings or nozzles on the body; -Corps.
Also, the valve can carry various auxiliary elements - devices for adjusting the tension of the springs or the stroke of the control device, drain fittings, handles for manual control of the flow of the working medium, switches for controlling other devices depending on the state of the valve, filters, etc.
Valves are divided into three groups according to the type and design of the control element:
- Spool - the control element is made in the form of a spool, which can distribute the flows of the working medium through the channels;
- Membrane - the control element is made in the form of an elastic membrane;
- Piston - the control element is made in the form of a piston adjacent to the seat.
In this case, the valve may have one, two or more control elements connected to one armature of the electromagnet.
The working principle of the solenoid valve is very simple. Consider the operation of the simplest two-way diaphragm normally closed valve used in fuel supply systems. When the valve is de-energized, the armature is pressed against the diaphragm by the action of a spring, which blocks the channel and prevents fluid from flowing further through the system. When current is applied to the electromagnet, a magnetic field arises in its winding, due to which the armature is drawn inward - at this moment the membrane, which is no longer pressed by the armature, rises under the influence of the pressure of the working medium and opens the channel. With the subsequent removal of current from the electromagnet, the armature under the action of the spring will return to its original position, press the membrane and block the channel.
Two-way valves work in a similar way, but they use either spools or piston-type control elements instead of a diaphragm. For example, consider the design and operation of the EPHX valve of carburetor cars. When the electromagnet is de-energized, the armature is lifted up under the action of the spring, and the locking element closes the upper fitting, connecting the side and lower (atmospheric) fittings - in this case, atmospheric pressure is applied to the EPHH pneumatic valve, it is closed and the carburetor idling system does not work. When current is applied to the electromagnet, the armature is retracted, overcoming the spring force, closes the lower fitting, while opening the upper one, which is connected to the engine intake pipe (where reduced pressure is observed) - in this case, a vacuum is applied to the EPHH pneumatic valve, it opens and turns on the idle system.
Solenoid valves are very reliable and unpretentious in operation, they have a significant resource (up to several hundred thousand actuations), and, as a rule, do not require special maintenance. However, in the event of a malfunction, any valve must be replaced as soon as possible - only in this case the necessary performance and safety of the vehicle will be ensured.
Post time: Aug-24-2023