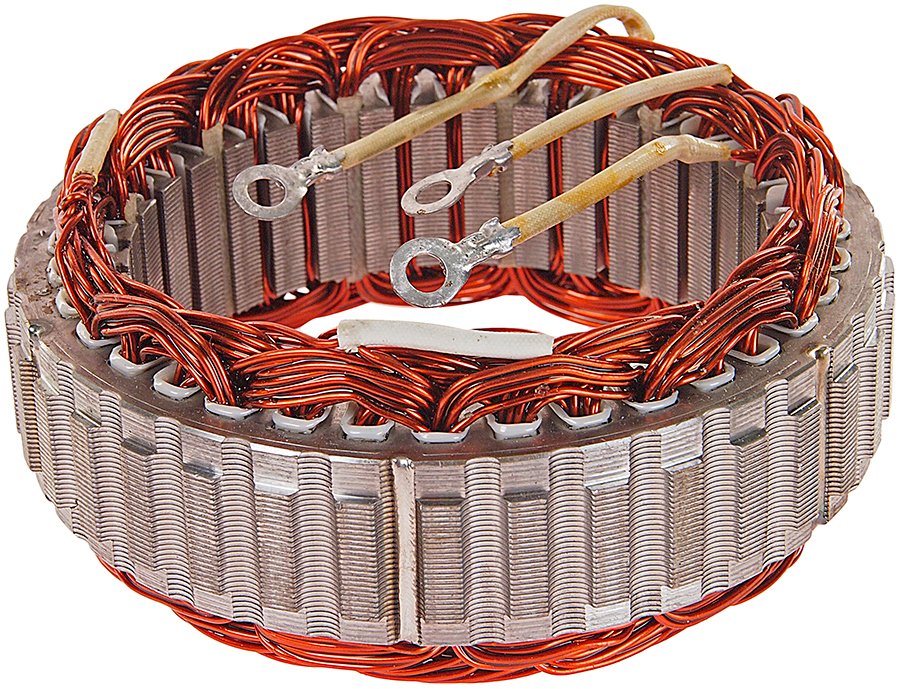
Every modern vehicle is equipped with an electric generator that generates current for the operation of the on-board electrical system and all its devices. One of the main parts of the generator is the fixed stator. Read about what a generator stator is, how it works and works in this article.
Purpose of the generator stator
In modern automobiles and other vehicles, synchronous three-phase alternators with self-excitation are used. A typical generator consists of a fixed stator fixed in a housing, a rotor with an excitation winding, a brush assembly (supplying current to the field winding), and a rectifier unit. All parts are assembled into a relatively compact design, which is mounted on the engine and has a belt drive from the crankshaft.
The stator is a fixed part of an automobile alternator that carries a working winding. During the operation of the generator, it is in the stator windings that an electric current arises, which is converted (rectified) and fed into the on-board network.
The generator stator has several functions:
• Carries a working winding in which an electric current is generated;
• Performs the function of a body part to accommodate the working winding;
• Plays the role of a magnetic circuit to increase the inductance of the working winding and the correct distribution of magnetic field lines;
• Acts as a heat sink - removes excessive heat from heating windings.
All stators have essentially the same design and do not differ in a variety of types.
Generator stator design
Structurally, the stator consists of three main parts:
• Ring core;
• Working winding (windings);
• Insulation of windings.
The core is assembled from iron ring plates with grooves on the inside. A package is formed from the plates, the rigidity and solidity of the structure is given by welding or riveting. In the core, grooves are made for laying the windings, and each protrusion is a yoke (core) for the winding turns. The core is assembled from plates with a thickness of 0.8-1 mm, made of special grades of iron or ferroalloys with a certain magnetic permeability. There may be fins on the outside of the stator to improve heat dissipation, as well as various grooves or recesses to dock with the generator housing.
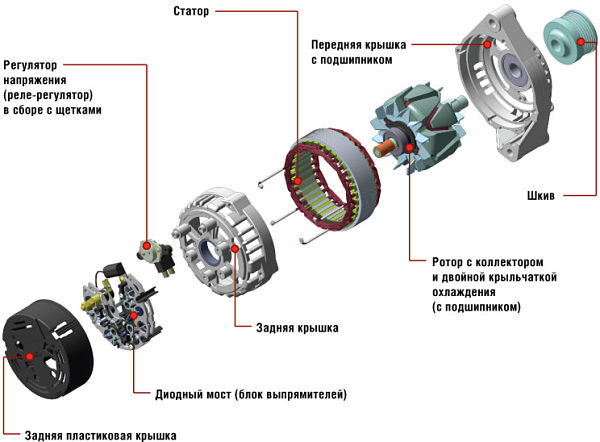
Three-phase generators use three windings, one per phase. Each winding is made of copper insulated wire of large cross-section (with a diameter of 0.9 to 2 mm or more), which is placed in a certain order in the grooves of the core. The windings have terminals from which alternating current is removed, usually the number of pins is three or four, but there are stators with six terminals (each of the three windings has its own terminals for making connections of one type or another).
In the grooves of the core there is an insulating material that protects the insulation of the wire from damage. Also, in some types of stators, insulating wedges can be inserted into the grooves, which additionally act as a fixator for the winding turns. The stator assembly can additionally be impregnated with epoxy resins or varnishes, which ensures the integrity of the structure (prevents the shift of turns) and improves its electrical insulating properties.
The stator is rigidly mounted in the generator housing, and today the most commonly used design is in which the stator core acts as a body part. This is implemented simply: the stator is clamped between two covers of the generator housing, which are tightened with studs - such a "sandwich" allows you to create compact designs with efficient cooling and ease of maintenance. The design is also popular, in which the stator is combined with the front cover of the generator, and the back cover is removable and provides access to the rotor, stator and other parts.
Types and characteristics of stators
The stators of the generators differ in the number and shape of the grooves, the scheme of laying the windings in the grooves, the wiring diagram of the windings and the electrical characteristics.
According to the number of grooves for the turns of the windings, stators are of two types:
• With 18 slots;
• With 36 slots.
Today, the 36-slot design is the most commonly used, as it provides better electrical performance. Generators with stators with 18 grooves today can be found on some domestic cars of early releases.
According to the shape of the grooves, stators are of three types:
• With open grooves - grooves of rectangular cross-section, they require additional fixation of the winding turns;
• With semi-closed (wedge-shaped) grooves - the grooves are tapered upwards, so the winding coils are fixed by inserting insulating wedges or cambrics (PVC tubes);
• With semi-closed grooves for windings with single-turn coils - the grooves have a complex cross-section for laying one or two turns of large-diameter wire or wire in the form of a wide tape.
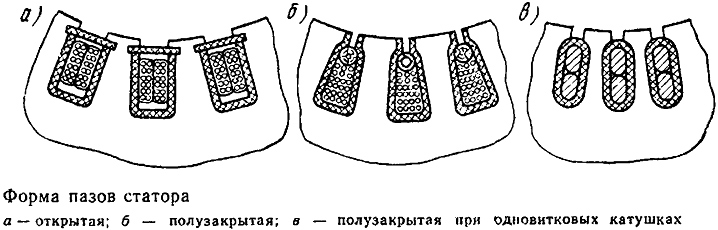
According to the winding laying scheme, stators are of three types:
• With a loop (loop distributed) circuit - the wire of each winding is placed in the grooves of the core with loops (usually one turn is laid in increments of two grooves, the turns of the second and third windings are placed in these grooves - so the windings acquire the shift necessary to generate a three-phase alternating current);
• With a wave concentrated circuit - the wire of each winding is placed in the grooves in waves, bypassing them from one side to the other, and in each groove there are two turns of one winding directed in one direction;
• With a wave distributed circuit - the wire is also laid in waves, but the turns of one winding in the grooves are directed in different directions.
For any type of stacking, each winding has six turns distributed over the core.
Regardless of the method of laying the wire, there are two schemes for connecting the windings:
• "Star" - in this case, the windings are connected in parallel (the ends of all three windings are connected at one (zero) point, and their initial terminals are free);
• "Triangle" - in this case, the windings are connected in series (the beginning of one winding with the end of the other).
When connecting the windings with a "star", a higher current is observed, this circuit is used on generators with a power of no more than 1000 watts, which work efficiently at low speeds. When connecting the windings with a "triangle", the current is reduced (1.7 times relative to the "star"), however, generators with such a connection scheme work better at high powers, and a conductor of a smaller cross-section can be used for their windings.
Often, instead of a "triangle", a "double star" circuit is used, in which case the stator should have not three, but six windings - three windings are connected by a "star", and two "stars" are connected to the load in parallel.
In terms of performance, for stators, the most important thing is the rated voltage, power and rated current in the windings. According to the nominal voltage, stators (and generators) are divided into two groups:
• With a winding voltage of 14 V - for vehicles with an on-board network voltage of 12 V;
• With a voltage in the windings of 28 V - for equipment with an on-board network voltage of 24 V.
The generator produces a higher voltage, since a voltage drop inevitably occurs in the rectifier and stabilizer, and at the entrance to the on-board power grid, a normal voltage of 12 or 24 V is already observed.
Most generators for cars, tractors, buses and other equipment have a rated current of 20 to 60 A, 30-35 A is enough for cars, 50-60 A for trucks, generators with a current of up to 150 or more A are produced for heavy equipment.
Working Principle of Generator Stator
The operation of the stator and the entire generator is based on the phenomenon of electromagnetic induction - the occurrence of current in a conductor that moves in a magnetic field or rests in an alternating magnetic field. In automobile generators, the second principle is used - the conductor in which the current arises is at rest, and the magnetic field is constantly changing (rotating).
When the engine starts, the generator rotor begins to rotate, at the same time voltage from the battery is supplied to its exciting winding. The rotor has a multi-pole steel core, which, when current is applied to the winding, becomes an electromagnet, respectively, the rotating rotor creates an alternating magnetic field. The field lines of this field intersect the stator located around the rotor. The stator core distributes the magnetic field in a certain way, its lines of force cross the turns of the working windings - due to electromagnetic induction, a current is generated in them, which is removed from the terminals of the winding, enters the rectifier, stabilizer and the on-board network.
With an increase in engine speed, part of the current from the stator working winding is fed to the rotor field winding - so the generator goes into self-excitation mode and no longer needs a third-party current source.
During operation, the stator of the generator experiences heating and electrical loads, and it is also exposed to negative environmental influences. Over time, this can lead to deterioration of the insulation between the windings and electrical breakdown. In this case, the stator needs to be repaired or completely replaced. With regular maintenance and timely replacement of the stator, the generator will serve reliably, stably supplying the car with electrical energy.
Post time: Aug-24-2023