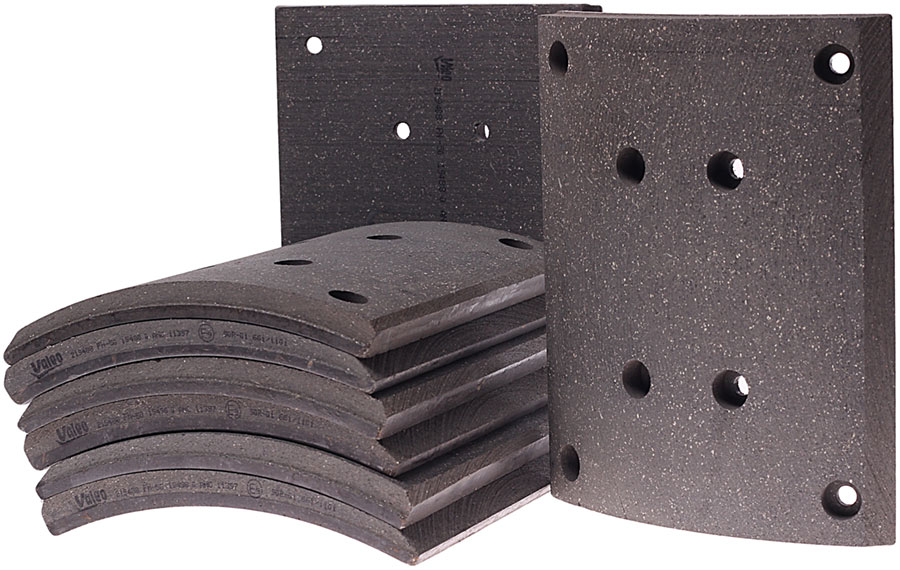
Each vehicle shall be equipped with a braking system, the actuators of which are brake pads in contact with the brake drum or disc. The main part of the pads is friction linings. Read all about these parts, their types, design and the right choice in the article.
What is a brake pad lining?
The brake pad lining (friction lining) is a component of the actuators of the brakes of vehicles, which ensures the creation of braking torque due to frictional forces.
The friction lining is the main part of the brake pad, it is in direct contact with the brake drum or disc when braking the vehicle. Due to the frictional forces arising from contact with the drum / disc, the lining absorbs the kinetic energy of the vehicle, converting it into heat and providing a decrease in speed or a complete stop. The linings have an increased coefficient of friction with cast iron and steel (from which brake drums and discs are made), and at the same time have high resistance to wear and prevent excessive wear of the drum / disc.
Today, there is a wide variety of brake pad linings, and for the correct choice of these parts, it is necessary to understand their classification and design.
Types and design of brake pad linings
Friction linings of brake pads can be divided into groups according to purpose, design and configuration, as well as the composition from which they are made.
According to the purpose, the pads are divided into two types:
• For drum brakes;
• For disc brakes.
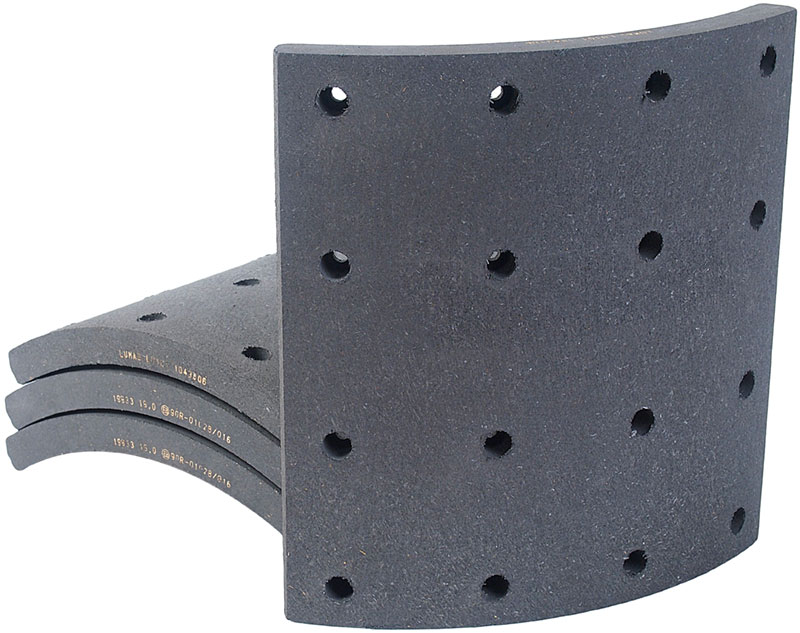
The drum brake pads are an arcuate plate with an outer radius corresponding to the inner radius of the drum. When braking, the linings rest against the inner surface of the drum, reducing the speed of the vehicle. As a rule, drum brake friction linings have a large working surface area. Each wheel brake mechanism is equipped with two linings located opposite each other, which ensures an even distribution of forces.
Disc brake linings are flat plates of crescent or other shapes that provide the maximum contact area with the brake disc. Each wheel brake mechanism uses two pads, between which the disc is clamped during braking.
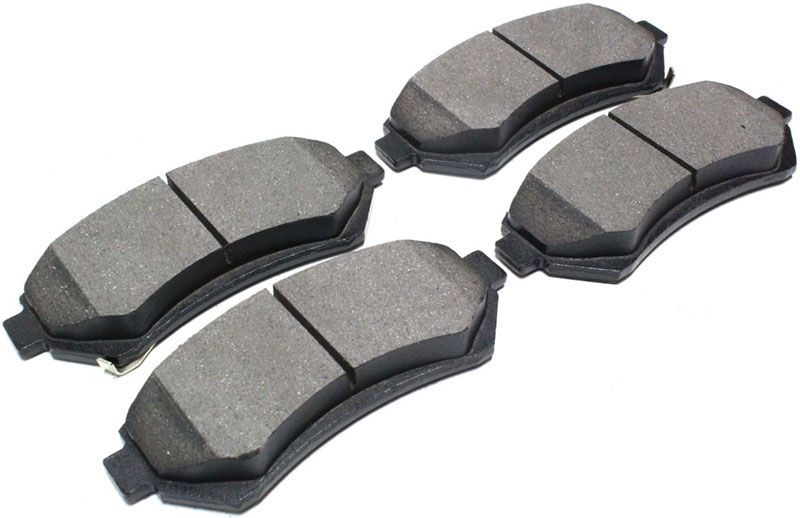
Also, brake pad linings are divided into two groups according to the place of installation:
• For wheel brakes - front, rear and universal;
• For the parking brake mechanism of trucks (with a drum on the propeller shaft).
Structurally, friction linings are plates molded from polymer compositions with a complex composition. The composition includes various components - frame-forming, filling, heat dissipating, binders and others. At the same time, all the materials from which the linings are made can be divided into two main groups:
•Asbestos;
• Asbestos-free.
The basis of asbestos linings are, as it is easy to understand, asbestos fibers (today it is a relatively safe chrysotile asbestos), which act as a plate frame that holds the rest of the components. Such pads are soft, but at the same time have a high coefficient of friction, they prevent excessive wear of the drum / disc and have a reduced noise level. In asbestos-free products, various polymer or mineral fibers play the role of the frame of the composition, such overlays comply with environmental standards, but are more expensive and in some cases have worse performance characteristics (they are more rigid, often noisy, etc.). Therefore, today asbestos friction linings are still widely used.
Various polymeric materials are used as fillers in the manufacture of overlays, polymers, resins, rubbers, etc. Additionally, ceramics, metal shavings (made of copper or other soft metals) for better heat dissipation, and other components may be present in the composition. Almost every manufacturer uses its own (sometimes unique) recipes, so the composition of friction linings can vary significantly.
Friction linings are manufactured using two main technologies:
• Cold pressing;
• Hot pressing.
In the first case, linings are formed from the finished mixture in special molds without additional heating. However, many manufacturers additionally use heat treatment of products after molding. In the second case, the mixture is pressed in heated (electric) molds. As a rule, with cold pressing, cheaper, but less durable linings are obtained, with hot pressing, products are of higher quality, but also more expensive.
Regardless of the method of production and composition, after manufacturing, the linings are polished and subjected to other additional processing. Friction linings go on sale in various configurations:
• Overlays without mounting holes and fasteners;
• Overlays with drilled mounting holes;
• Overlays with holes and a set of fasteners;
• Complete brake pads - linings mounted on the base.
Friction linings of brake pads without holes are universal parts that can be adjusted to the brake pads of various cars, which have the appropriate dimensions and radius. Overlays with holes are suitable for certain car models, it is possible to install them on pads with a different arrangement of holes only after additional drilling, or it is completely impossible. Overlays complete with fasteners facilitate the installation process and help ensure the highest quality result.
Complete brake pads are already a separate type of spare parts, they are used in the repair of disc brakes, drum mechanisms with pads glued to the pads, or badly worn drum mechanisms. On trucks, such components are rarely used.
Friction linings are installed on the brake pads with rivets (solid and hollow) or on glue. Rivets are used in drum brakes, glue is most commonly used in disc brake pads. The use of rivets provides the ability to replace the linings as they wear out. To prevent damage to the brake drum or disc, rivets are made of soft metals - aluminum and its alloys, copper, brass.
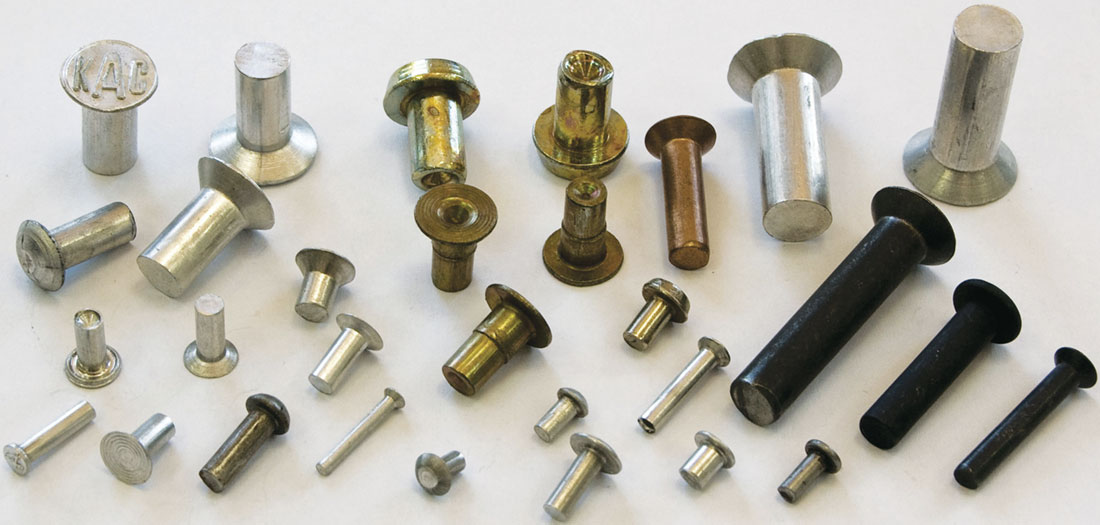
Mechanical and electronic wear sensors can be installed on modern brake pad linings. A mechanical sensor is a plate in the body of the lining, which, when the part wears out, begins to rub against the drum or disc, making a characteristic sound. The electronic sensor is also hidden in the body of the lining, when it is worn, the circuit is closed (through a disk or drum) and the corresponding indicator lights up on the dashboard.
Correct selection, replacement and operation of brake pad linings
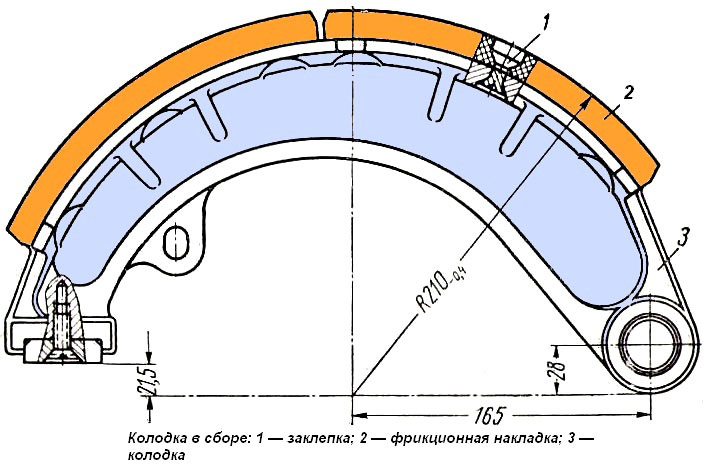
Friction linings are subject to wear during operation, their thickness gradually decreases, which leads to a decrease in the reliability of the brakes. As a rule, one lining serves 15-30 thousand kilometers, after which it must be replaced. In difficult operating conditions (increased dustiness, movement on water and dirt, when working under high loads), the replacement of linings should be performed more often. The linings should be changed when they are worn to the minimum allowable thickness - it is usually at least 2-3 mm.
For replacement, it is necessary to use friction linings that have dimensions suitable for a particular car - width, length and thickness (all the necessary parameters are usually indicated on the linings). Only in this case, the lining will be fully pressed against the drum or disc and sufficient braking force will be created. For mounting the pad on the block, you can use only rivets made of soft metals, it is better to give preference to fasteners in the kit. The rivets should be buried in the body of the linings to prevent them from rubbing against the drum, otherwise the parts will be subject to intense wear and tear and may fail.
It is necessary to change the linings on the brake pads in complete sets, or, in extreme cases, both on the same wheel - this is the only way to ensure the normal operation of the brake mechanisms. It is necessary to carry out the replacement in full accordance with the instructions for repair and maintenance of a particular car, otherwise there is a high probability of deterioration of the brakes.
When operating the car, you should avoid overheating of the linings, as well as their wetting and contamination - all this reduces their resource and increases the likelihood of breakdowns. When driving through water, the linings need to be dried (accelerate several times and press the brake pedal), with long descents, it is recommended to resort to engine braking, etc. With proper operation and timely replacement of the linings, the car's brakes will work reliably and safely.
Post time: Aug-22-2023